Denver Precision Products’ Factors for Successful Knurling
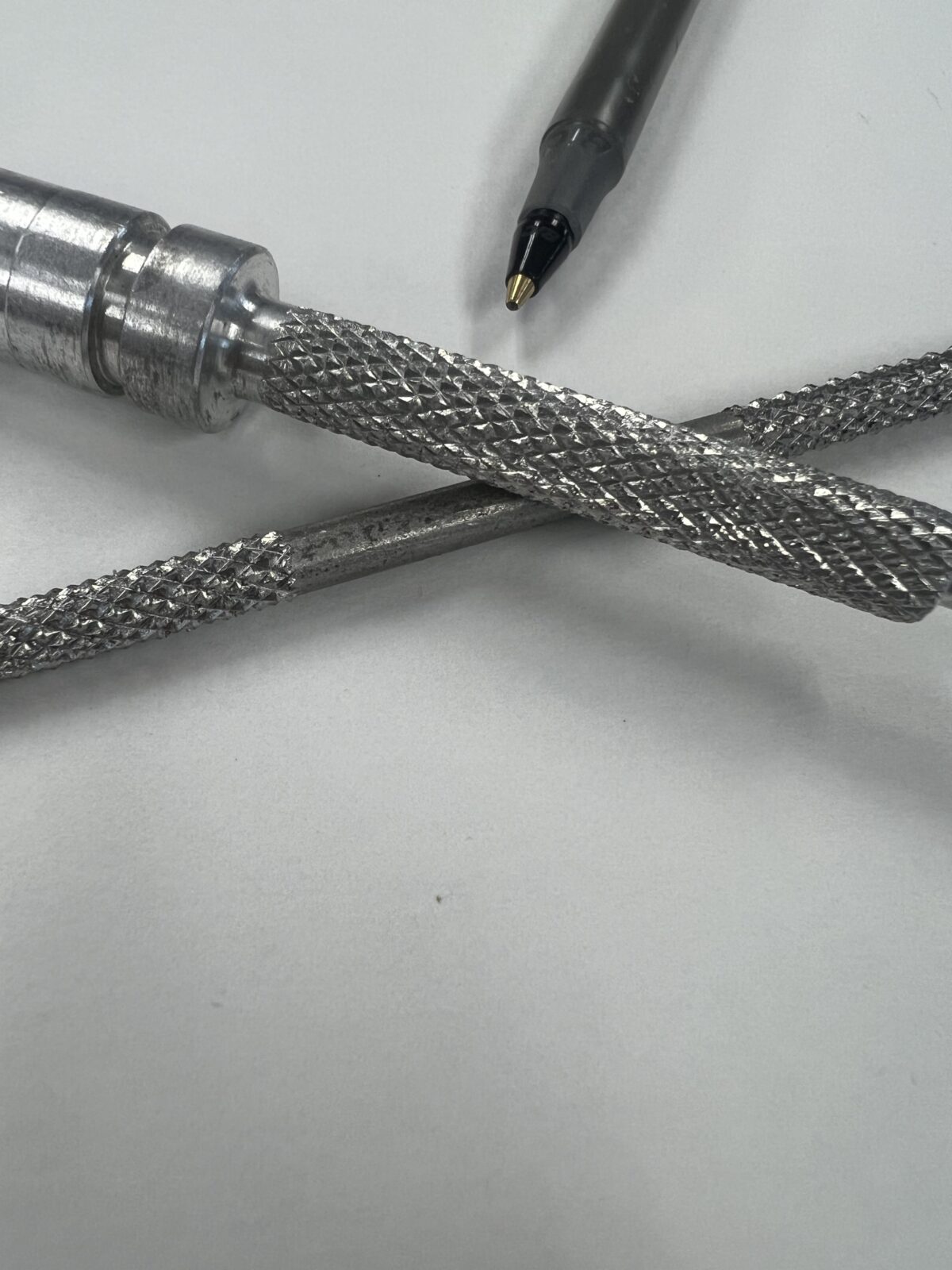
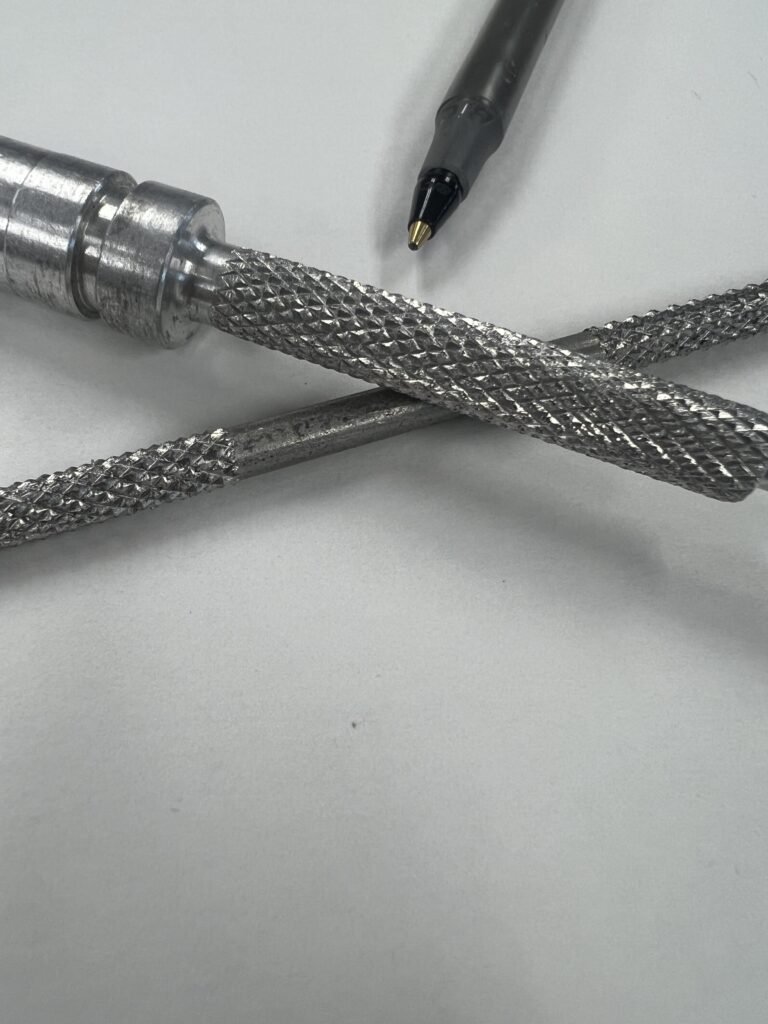
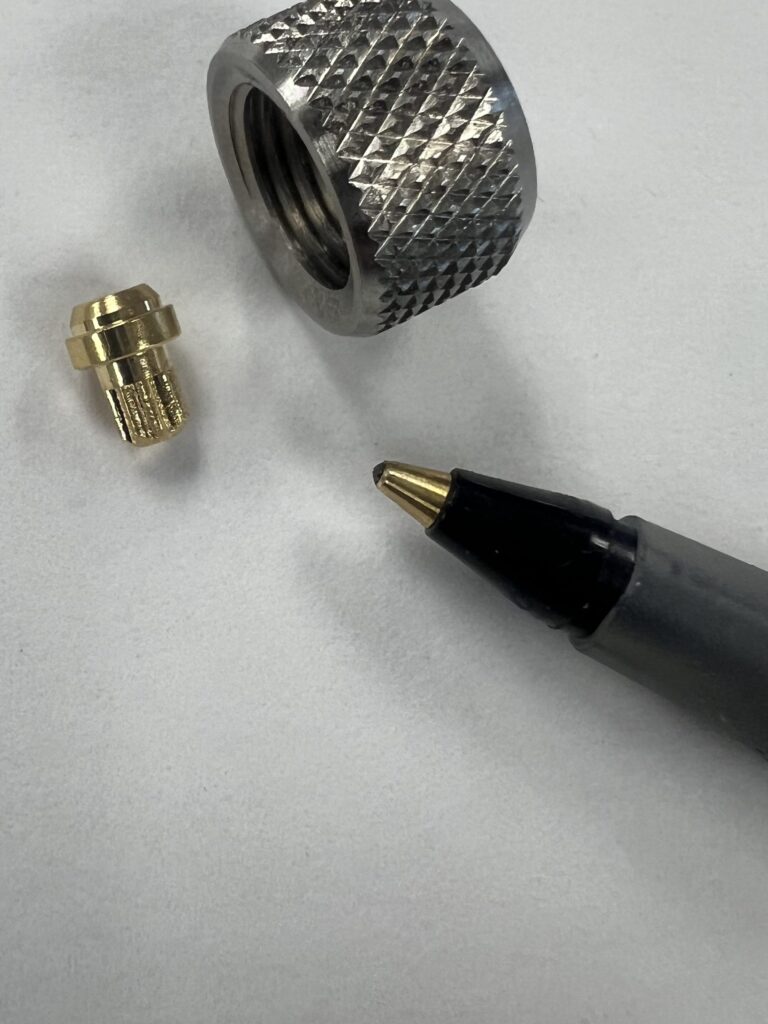
Knurling is a machining process used to create a textured pattern on cylindrical surfaces for better grip or aesthetics, or press fit needs. The type of knurling that Denver Precision Products uses is created by using a special tool called a knurling wheel. This is forming process that displaces material from a die onto the part. Common knurl patterns include straight, diamond, and cross-hatch designs.
Several factors influence the success of the knurling process:
- Material Selection: Softer materials like aluminum, brass, and mild steel are easier to knurl, while harder materials may require sharper knurl wheels and greater precision.
- Tooling and Alignment: Proper tool selection, sharp knurling wheels, and precise alignment with the workpiece’s centerline are critical for achieving clean patterns.
- Operating Parameters: Slow spindle speeds and appropriate pressure ensure consistent pattern depth without damaging the workpiece.
Challenges and Solutions
Common issues in knurling include double-tracking, where patterns overlap due to a mismatch between the tool pitch and the workpiece circumference, and crushing, which occurs when excessive pressure deforms the material instead of embossing the pattern. These problems can be mitigated by ensuring proper setup, using the right tools, and applying cutting fluid to reduce friction and heat.
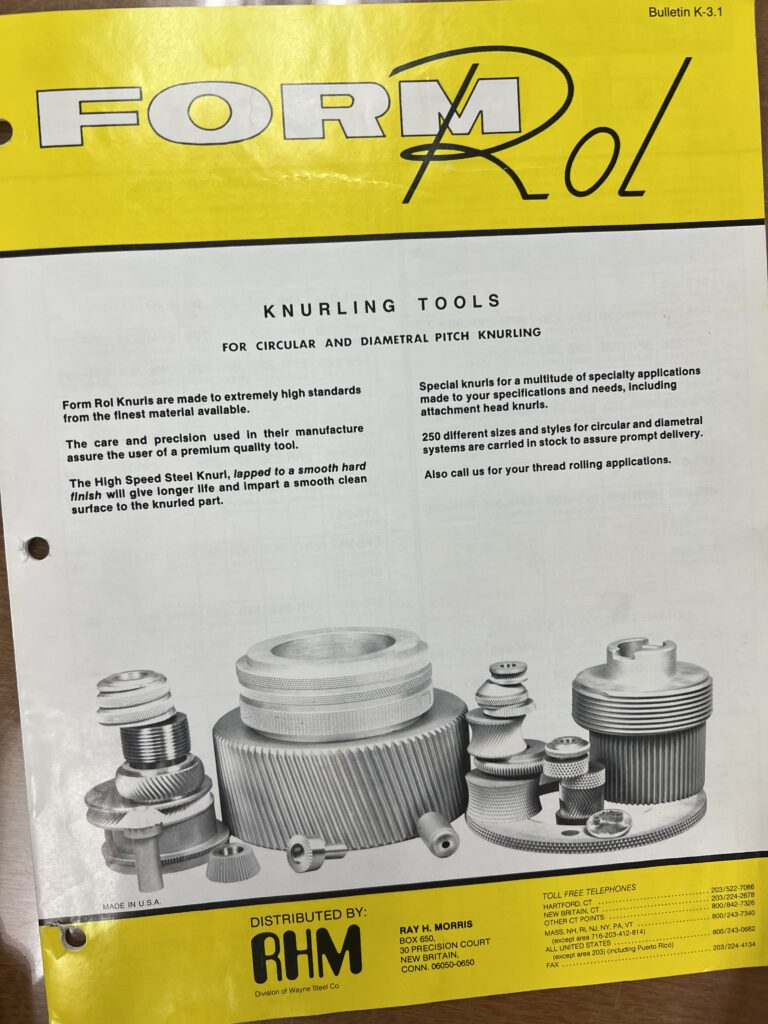
Challenges | Solutions |
DOUBLE TRACKING | CHECK THE PRESURE THE KNURL IS FORMING, INCREASE PRESURE |
FLAKING KNURL | NEED TO CHECK TRACKING OF KNURL |
BROKEN KNURL FORM | TOO MUCH PRESURE ON THE KNURL WHEEL |
Conclusion
Knurling is a versatile machining process that combines functionality and aesthetics. Its applications range from everyday tools to precision-engineered components, making it an invaluable technique in manufacturing. With proper setup, material selection, and attention to detail, knurling can deliver high-quality results that enhance both the usability and appearance of machined products.